Tips for Caring for Bidriware Art
When you invest in such precious and beautiful artwork, it is important to take care of it properly to ensure that it lasts long.
It should be cleaned only with water, and no soap or detergent should be used. The use of harsh chemicals can damage the surface of the artwork.
Dust should not be allowed to settle on it. Bidriware handicrafts should be dusted regularly with a soft cloth.
The shine of bidriware art can be maintained by just applying vegetable oil. Scratches and abrasions on the surface should be avoided.
The Story of Bidriware Art : Exploring its Past and Present
India is a big cauldron of heritage that is ever bubbling with the most breathtaking forms of art, and one of them is the bidriware art. This art form originated in Persia, but between the 14th and 15th centuries, the craft made its way to India. The Bahamani Sultans nurtured its growth in the country. Many bidriware craft products like hookahs, spittoons, pan holders, etc., graced the royal courts of that time.
Currently, bidriware art is practiced in Bidar, Karnataka, by the most skilled artisans to make products, including vases, ornaments, jewelry boxes, trays, statues, etc. These craftsmen have been doing this for generations and have made this art what it is today. With the advent of technology, many art forms took a hit, and so did bidriware. With people preferring machine manufactured products, the demand for handicrafts started dwindling, impacting the artisans' livelihood. However, the recent issue of a Geographical Indication (GI) tag by the Government of India for Bidriware artisans has given them a major push.
Making bidriware crafts involves the inlay of gold and silver wires in an alloy of copper and zinc. One of its main attractions is the awe-inspiring contrast between the black and the silver. Another eye-catching feature is the fine detailing on each piece. The bidriware designs are dominated by floral patterns, leaves, and geometrical designs, which reflect Persian artistry. It takes hours of undivided focus and precision to bring bidriware handicrafts to life. This is a very long and tedious process and involves 8 stages.
Making of Bidriware Crafts
The first step is molding red clay into the shape the artisans desires and pouring the molten metal into it. An alloy of copper and zinc is used in the 16:1 ratio.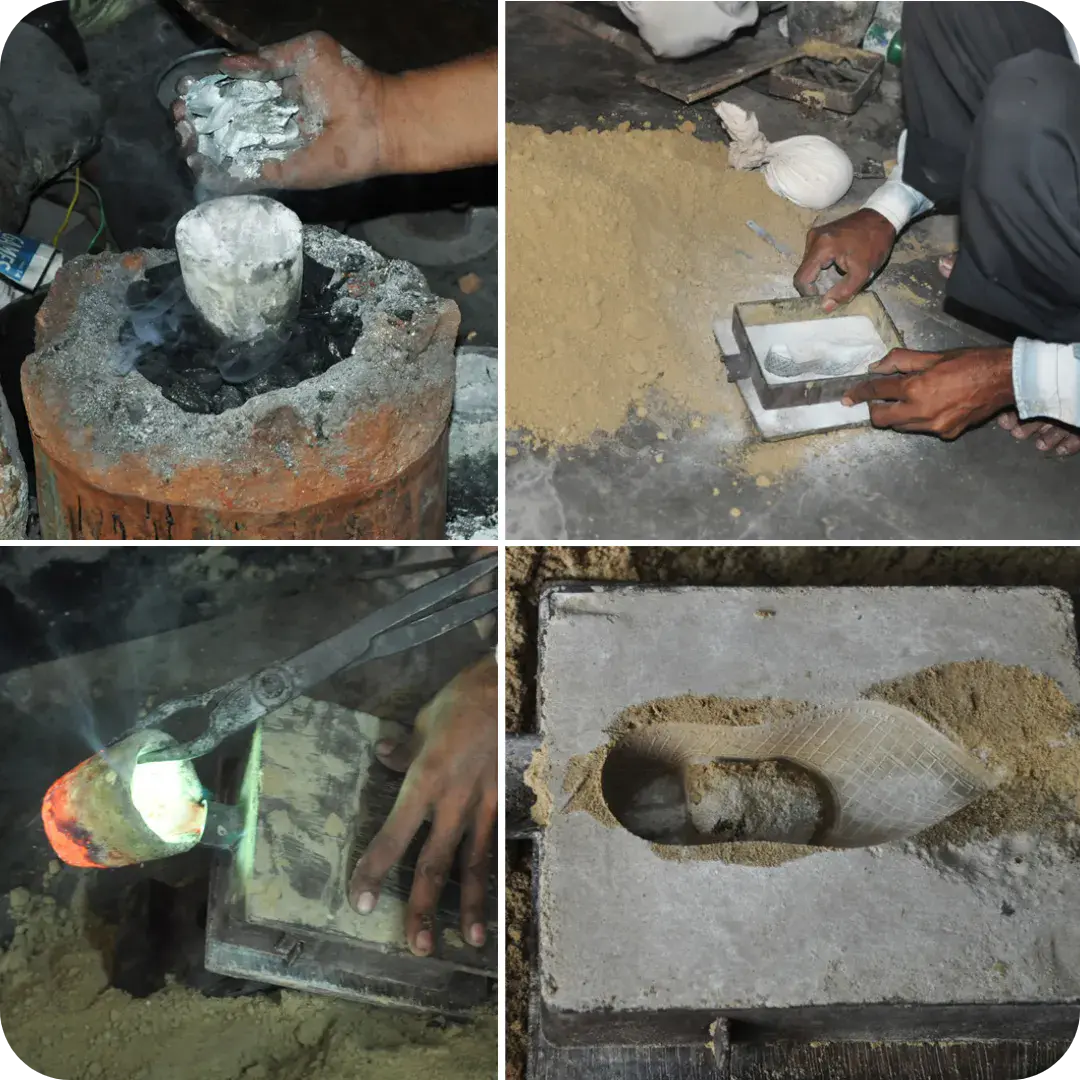
The second stage involves removing the clay and smoothing the surface of the shaped metal with fine-quality sandpaper.
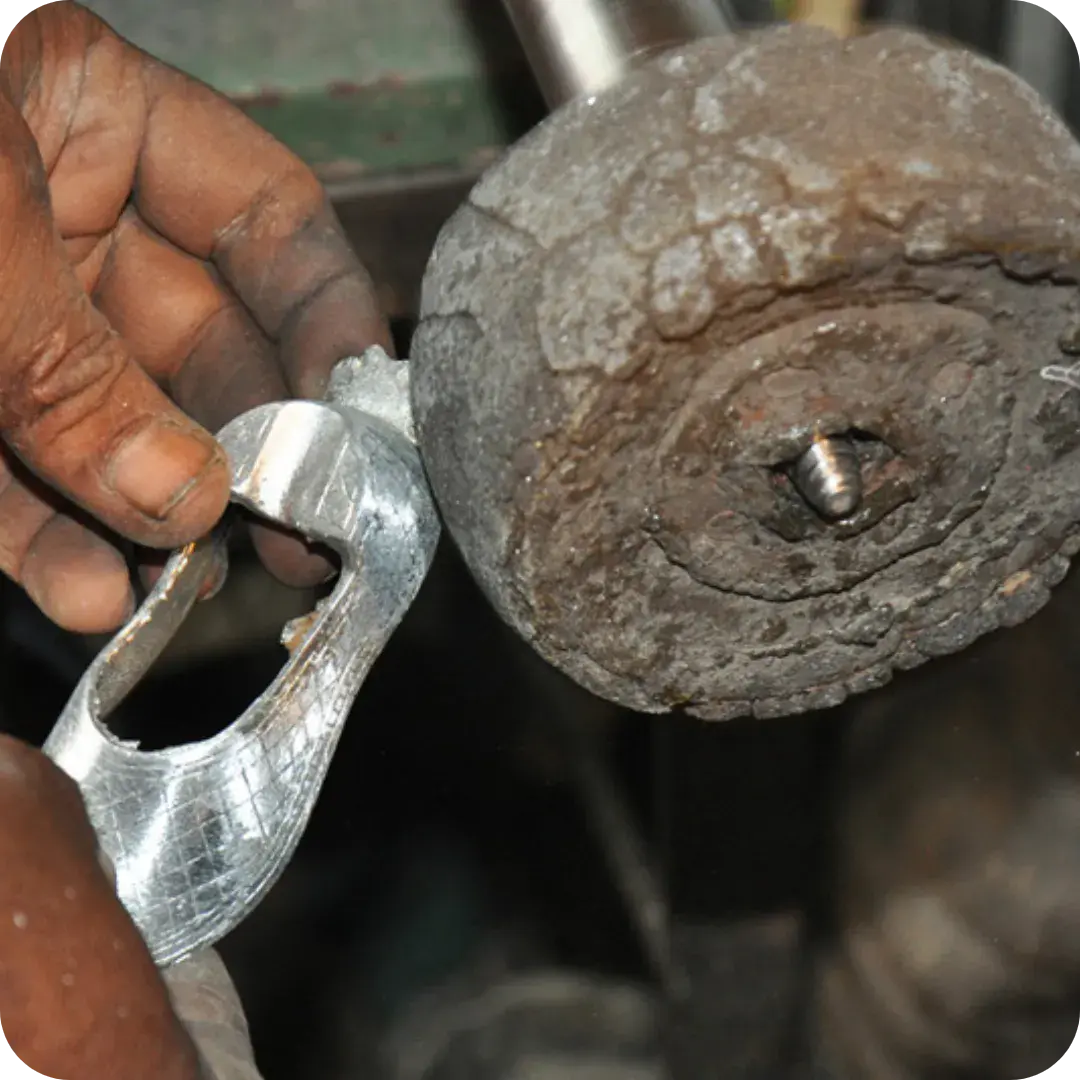
In the third stage, the design is carved on the surface of the metal with a sharp object.
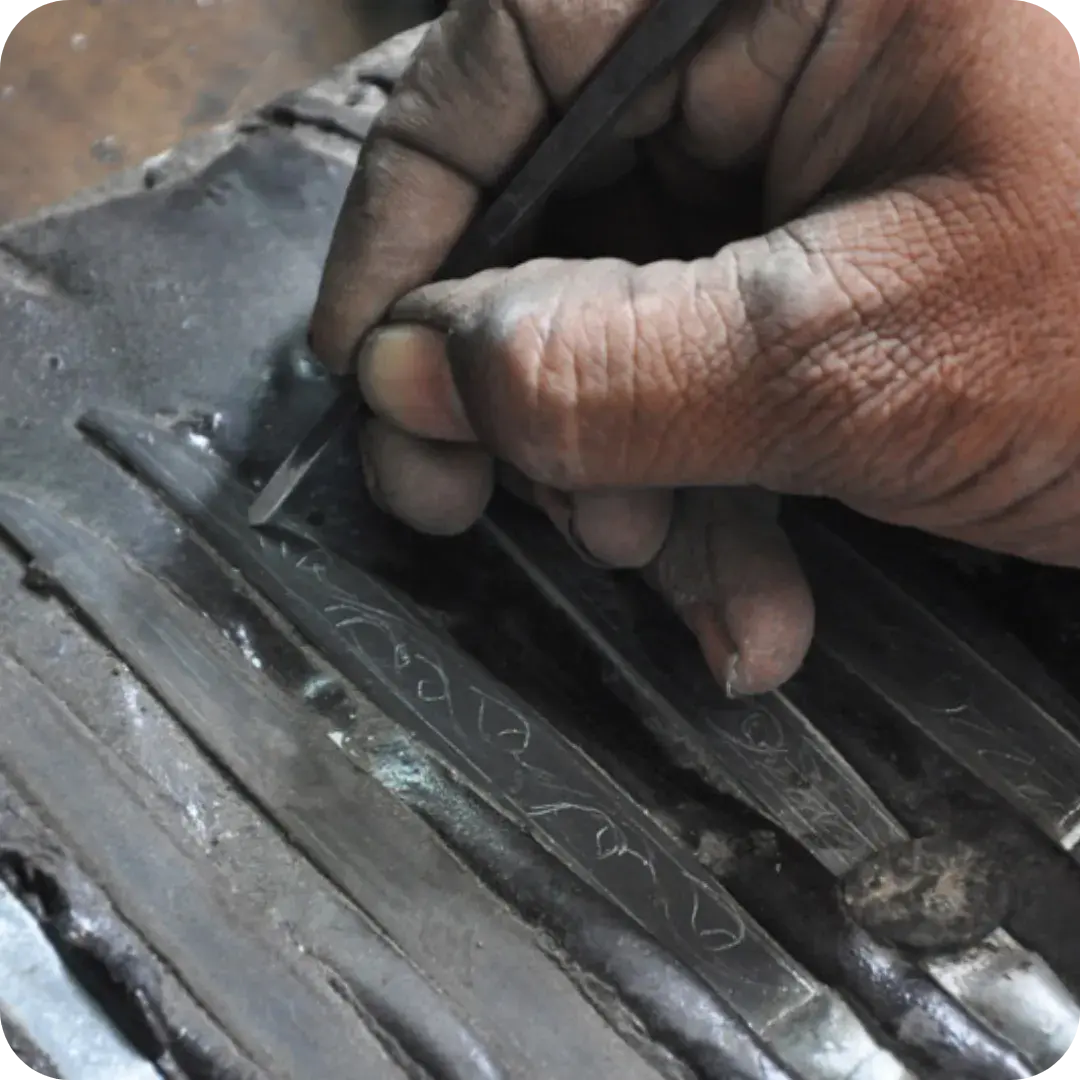
The fourth step involves inlay work. Sheets or wires of silver or sometimes even gold are hammered in the groves of the carved design.
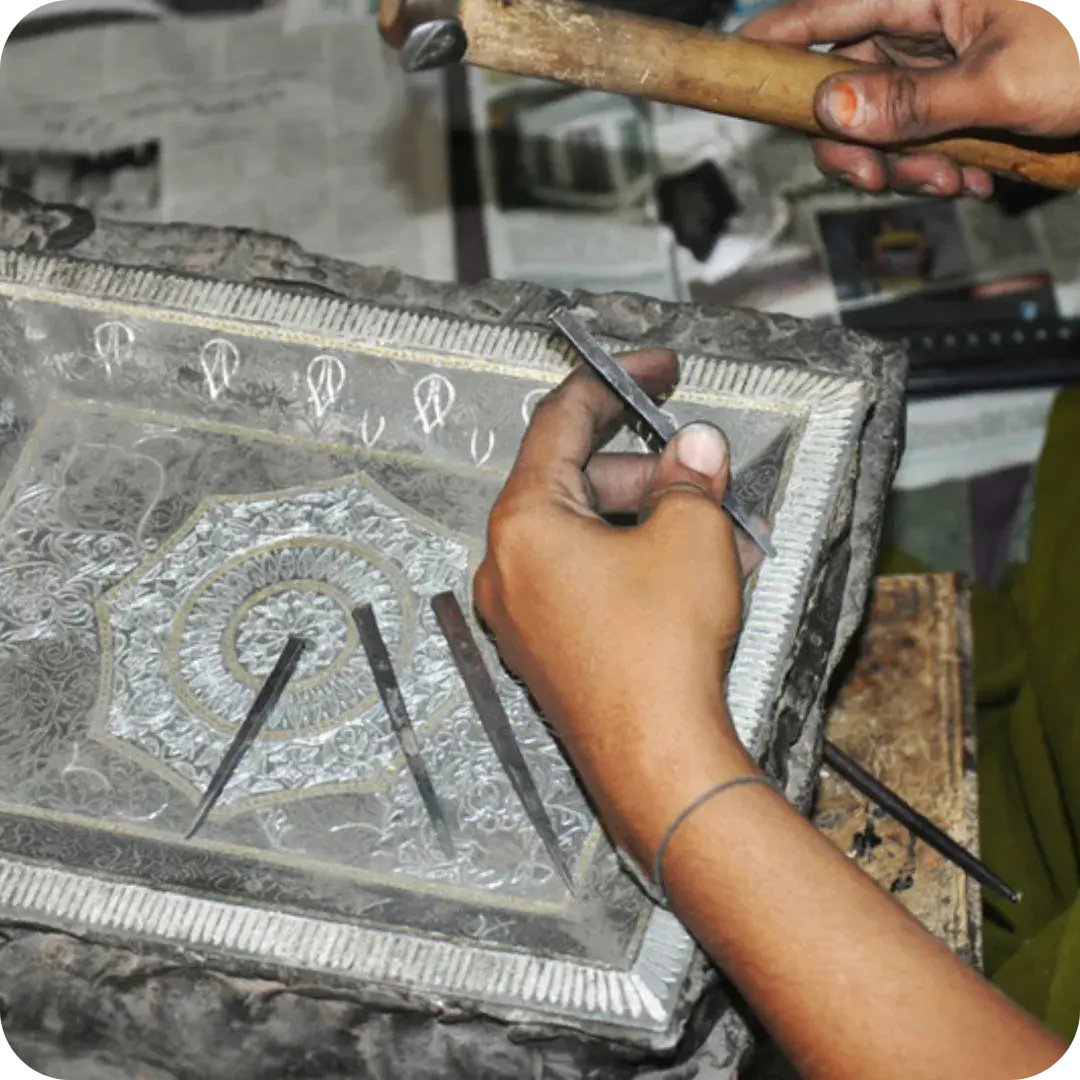
In the fifth stage, the object is smoothened using a buffing machine to remove any bumps and unevenness.
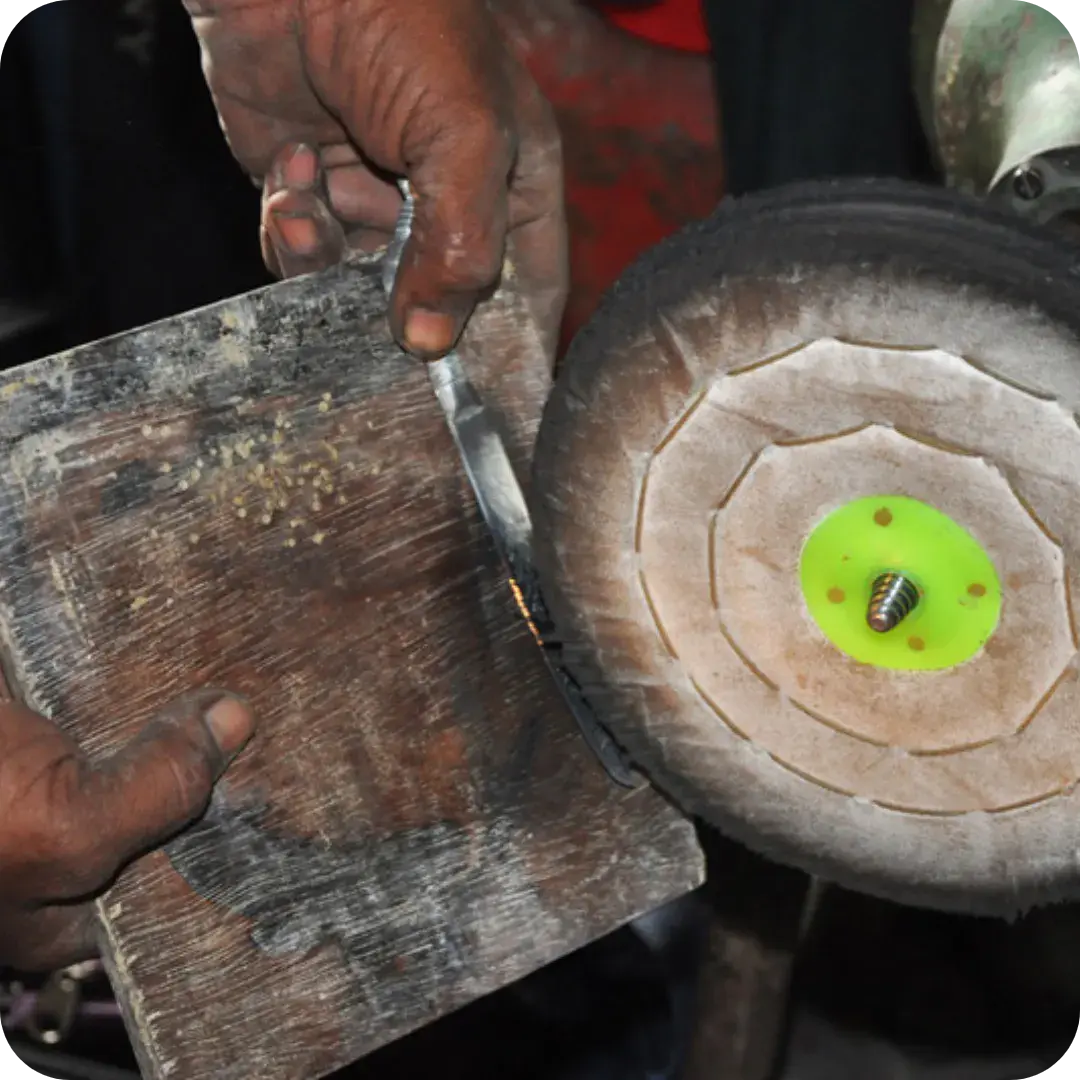
At the sixth stage, the product is dipped in a mixture of the soil of Bidar fort, ammonium chloride, and water. This soil has oxidizing properties which turn zinc completely black to create a beautiful contrast with silver.
Finally, at the seventh step, the paste is removed and oil is rubbed to intensify the black coating of the metal.
